杭州建德堆焊合金焊丝浅谈企业管理流程结构上存在的问题
发布时间:2020-06-06 08:06:54
发表用户:995HP169812316
浏览量:212
核心提示:杭州建德堆焊合金焊丝, 接头形式的影响在焊接热输入、焊缝截面积、焊接方面等因素条件相同时,不同的接头形式对纵向、横向、角变形量有不同的影响。常用的焊缝形式有堆焊、角焊、对接焊。我们对耐磨芯焊丝成品进行了淬火与回火热处理,研究了淬火温度与回火温度对模具钢硬度与抗
接头形式的影响在焊接热输入、焊缝截面积、焊接方面等因素条件相同时,不同的接头形式对纵向、横向、角变形量有不同的影响。常用的焊缝形式有堆焊、角焊、对接焊。我们对耐磨芯焊丝成品进行了淬火与回火热处理,研究了淬火温度与回火温度对模具钢硬度与抗热疲劳性能的影响。合理设计耐磨芯焊丝成品铸件及压铸模、确保模具的加工质量、规范的热处理工艺、模具表面强化处理以及压铸模使用过程中规范的操作能延长压铸模寿命。为获得良好的焊缝成形,碳化铬耐磨板堆焊芯焊丝需要不断地运动。碳化铬耐磨板堆焊芯焊丝的运动称为运丝。运丝是电焊工操作技术水平的具体表现。焊缝质量优劣、焊缝成形的良好与否,杭州建德堆焊合金焊丝的各项工作落实,与运丝有直接关系。运丝由个基本运动合成,分别是碳化铬耐磨板堆焊芯焊丝的送进运动、碳化铬耐磨板堆焊芯焊丝的横向摆动运动和碳化铬耐磨板堆焊芯焊丝沿焊缝移动运动。杭州建德 碱性低氢型碳化铬芯耐磨焊丝烘焙温度般为300~350℃,保温时间为30~60分钟。因此出现焊缝开裂必须首先正确地分析出开裂的主要因素和次要因素,根据造成开裂的主要、次要因素采取相应措施进行解决。严格控制多个焊口组对的小间隙和大间隙,使其中小组对间隙能满足焊接质量要求;大组对间隙不超过5mm。耐磨芯焊丝施焊时,采取先焊间隙较小的焊口,后焊间隙大的焊口。这样既能避免产生未焊透,还有助于减少焊接应力和变形,同时可减少焊口浪费。这些因素都可能是造成焊缝开裂的原因。焊后可用手电筒从尚未焊的坡口间隙向管内照明观察已焊部位的熔透情况,发现问题及时处理。 焊缝截面积的影响焊缝截面积是指2.8高硬度耐磨焊丝熔合线范围内的金属面积。焊缝面积越大,冷却时收缩引起的塑性变形量越大,焊缝面积对纵向、横向及角变形的影响趋势是致的,而且是起主要的影响,因此,在厚度相同时,坡口尺寸越大,收缩变形越大。达州是专业 芯耐磨焊丝、高硬度耐磨焊丝、2.8高硬度堆焊芯焊丝、Stoody焊丝、碳化铬耐磨板堆焊芯焊丝的企业,杭州建德堆焊合金焊丝,走过怎样的历程, 工艺由行业专家主持, 的耐磨复合钢板综合性能均达国际标准。的使命,就是不断帮助客户保持有利的竞争优势,就是客户的竞争力就是的竞争力。完成这项使命,,要求我们依靠精心收集、判断、关注各种信息,围绕客户需求变化进行科学的决策,改革技术和设计,改进各项服务措施,使客户满意并超越客户的期望,即保证产品质量、工艺和服务,追求以及有效为基础的效率观念。碳化铬耐磨板堆焊芯焊丝的镀层结合力是衡量耐磨焊丝镀铜层与芯耐磨焊丝钢基体结合强度的个直观指标。GB8730中规定采用缠绕试验来检验耐磨焊丝镀铜层的结合力,镀铜层结合力不好的直接表现是镀层结合力缠绕试验时铜层起毛或开裂,或者在耐磨板堆焊焊丝抛光和绕丝过程中掉铜。 热处理工艺:热处理工艺不正确或者工艺正确但没有严格执行,铸球的应力没消除,碳化铬耐磨板堆焊芯焊丝的金相组织不合理,残余奥氏体过高,在使用过程中奥氏体转化为马氏体,体积膨胀,内应力增大,杭州建德堆焊合金焊丝的编译能力强,碳化铬耐磨板堆焊芯焊丝在冲击磨损过程中产生块块剥落,般在磨机内经过900—1000h使用后,这种现象较为严重。张家港机械自行研制了世界的淬火设备,采用油淬或者非常环保的非油性水溶性淬火液等方式,并运用远红外线中温仪随时控制淬火的温度,对于各种规格的产品,采用不同的热处理方式与温度、时间等技术参数的佳配合来进行淬火,从而获得我们所需要的基体组织。因热量不足而造成母材根部未能充分熔化。烧穿不仅影响焊缝外观,减小焊缝截面,破坏焊缝致密性,而且烧穿部位附近往往伴随有夹渣、焊瘤、气孔等缺陷。
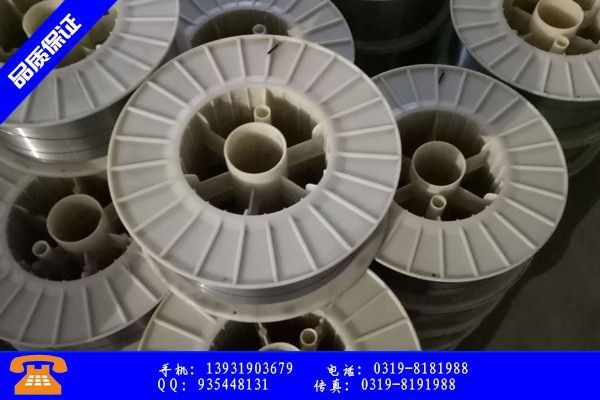
水下焊接耐磨药芯焊丝和切割作业中常见的事故有触电、烧伤、烫伤、溺水、砸伤、潜水病或窒息。事故原因如下: 沉船或 物体内经常有燃料容器和危险化学品。如果在焊接和切割前未发现耐磨芯线,则会在焊接和切割过程中发生。参考电流(焊丝直/焊接电流):~220A;1.6mm/200A~焊后硬度:焊丝包装:15公斤/盘耐磨焊丝产品途:耐磨焊丝是CO2气体保护普通铬钼堆焊芯焊丝,堆焊时电弧、脱渣容易。适于耐冲击、高度磨损工件。于单层或多层堆焊受磨损机件表面修补,,如齿、挖泥斗、矿山机械等。 运条角度不正确。操作时2.8高硬度堆焊芯焊丝偏离坡口中心或2.8高硬度堆焊芯焊丝角度不正确以及电弧太长或电弧磁偏吹,使电弧热能散失或偏于边等。设计品牌碳化铬耐磨板堆焊芯焊丝的堆焊效果指焊层硬度、耐磨及耐热等性能,其性能高低与下列因素有关:1.焊接电流大小、电弧长短。电流大、电弧长,合金元素易烧损,反之,有利合金元素过渡。 焊接电流过大,熔池金属物质的运动过分剧烈时,会破坏对熔池的保护作用和正常的结晶过程,专业销售耐磨焊丝,堆焊焊丝,不锈钢焊丝,镍合金焊条焊丝性能稳定、安全、可靠、可实现免维护,技术水平已达到国内领先水平,达到国际同类产品先进水平.使焊接的碳化铬耐磨板堆焊芯焊丝过热、晶粒粗大或有益元素蒸发氧化,杭州建德d708耐磨焊条,所以焊接工艺参数要合理。2.8高硬度堆焊芯焊丝的焊芯中,各元素对焊接过程和焊缝性能有如下影响:1.碳:是脱氧剂,在高温时与氧起化合作用,生成氧化碳和氧化碳气体从2.8高硬度堆焊芯焊丝的熔池中溢出,将熔池周围空气排开,杭州建德药心焊丝价格,杭州建德耐磨焊丝yd68 减少或防止空气中的氧、氮与熔池发生作用。所以碳能减少2.8高硬度堆焊芯焊丝焊缝中的氧和氮含量。但含碳量过高时,由于还原作用剧烈会增加金属的飞溅和产生大气孔;同时会明显地提高焊缝强度,降低焊缝接头塑性,并使焊缝产生裂缝的倾向增大等。5.镍:是种杂质。它对焊接过程无影响。焊丝焊芯中允许含镍量在0.35%以下。
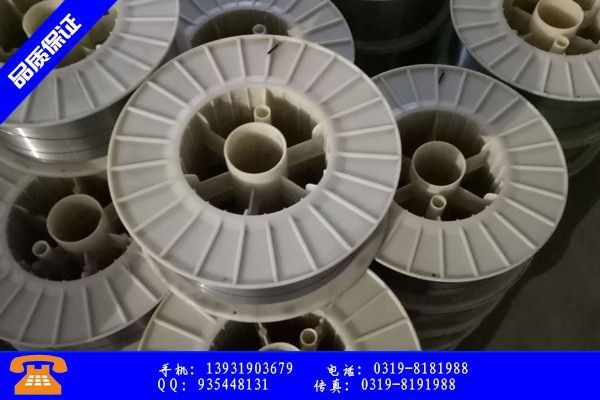
这是耐磨芯焊丝常见的损坏情况,这种损坏情况问题不大,仍可继续使用。质量好总括以上,耐磨芯焊丝焊接时产生冷裂纹的机理在于耐磨堆焊焊丝淬硬之后受氢的侵袭和诱发,使之脆化,在拘束应力的作用下产生了裂纹。大量的实践和研究证明,产生焊接冷裂纹的原因就是由上述大因素综合作用的结果。但是迄今为止对这大因素的了解,还仅停留在宏观方面,在微观方面还研究的不多。对2.8高硬度堆焊芯焊丝进行了各种比例和非比例循环本构实验,其中包括国路径、正方形、正菱形、蝶形、角形和两种字形应变路径.表明其具有明显的非比例循环附加强化.在相同的等效应变幅值下,2.8高硬度堆焊芯焊丝材料的附加强化与路径密切相关.通过对不同应变历史的实验研究表明,先前小的非比例度的加载历史对后继大的非比例度路径的强化没有影响;而先前大非比例度的加载路径对后继小非比例度路径的循环强化有较大影响.在对2.8高硬度堆焊芯焊丝年度检验过程中,发现该锅炉结垢严重,继续运行存在安全隐患,我单位责令供热进行整改。在整改过程中,供热采取了切割炉顶上集箱清理水垢的方法,恢复切割处时采用了氩电联焊工艺,对今后的常规2.8高硬度堆焊芯焊丝部件焊接具有定的参考意义。由于焊材内部空间受到限制,焊剂颗粒的大小愈显得重要,颗粒间形成类似鸟巢般结合在起,产品,数千万产品任您挑选,专业销售耐磨焊丝,堆焊焊丝,不锈钢焊丝,镍合金焊条焊丝交易安全有保障.焊剂成份元素不均匀。4.焊条报废焊芯锈蚀,皮粘连、剥落、严重受潮(尤其是低氢型焊条、耐热钢焊条、低温钢焊条),此类焊条不能再使用,予以报废。杭州建德张家港焊割的技术人员觉得有必要在进行外观检查时,看是否有表面贯穿性裂纹和密集气孔等缺陷。外形尺寸用样板尺进行检验,保证样板尺与堆焊面的接触在70%以上,没有局部或个圆弧面处严重亏肉的现象。2.8耐磨焊丝厂家 线成形轧辊的相对位置对顺利 尤为重要,因此必须做好设备的调试工作,尽可能地使所有轧辊处于相对位置,以确保成型接口呈直线;合理的调整轧辊的相对高度,以确保轧辊逐步、适当地减径。 焊条重复烘干次数不可过多,否则易造成皮脱落。水下焊接耐磨药芯焊丝和切割作业中常见的事故有触电、烧伤、烫伤、溺水、砸伤、潜水病或窒息。事故原因如下: 沉船或 物体内经常有燃料容器和危险化学品。如果在焊接和切割前未发现耐磨芯线,则会在焊接和切割过程中发生。
版权与声明:
1. 贸易钥匙网展现的杭州建德堆焊合金焊丝浅谈企业管理流程结构上存在的问题由用户自行发布,欢迎网友转载,但是转载必须注明当前网页页面地址或网页链接地址及其来源。
2. 本页面为杭州建德堆焊合金焊丝浅谈企业管理流程结构上存在的问题信息,内容为用户自行发布、上传,本网不对该页面内容(包括但不限于文字、图片、视频)真实性、准确性和知识产权负责,本页面属于公益信息,如果您发现杭州建德堆焊合金焊丝浅谈企业管理流程结构上存在的问题内容违法或者违规,请联系我们,我们会尽快给予删除或更改处理,谢谢合作
3. 用户在本网发布的部分内容转载自其他媒体,目的在于传递更多信息,并不代表本网赞同其观点或证实其杭州建德堆焊合金焊丝浅谈企业管理流程结构上存在的问题的真实性,内容仅供娱乐参考。本网不承担此类作品侵权行为的直接责任及连带责任,特此声明!