兴仁市yd688耐磨焊丝价格仍现倒挂厂调控略有不利
发布时间:2020-07-25 04:16:01
发表用户:995HP169812316
浏览量:598
核心提示:兴仁市yd688耐磨焊丝,4.焊条报废焊芯锈蚀,皮粘连、剥落、严重受潮(尤其是低氢型焊条、耐热钢焊条、低温钢焊条),此类焊条不能再使用,予以报废。碳化铬耐磨板堆焊芯焊丝的堆焊效果指焊层硬度、耐磨及耐热等性能,其性能高低与下列因素有关:1.焊接电流大小、电弧长短。电流
4.焊条报废焊芯锈蚀,皮粘连、剥落、严重受潮(尤其是低氢型焊条、耐热钢焊条、低温钢焊条),此类焊条不能再使用,予以报废。碳化铬耐磨板堆焊芯焊丝的堆焊效果指焊层硬度、耐磨及耐热等性能,其性能高低与下列因素有关:1.焊接电流大小、电弧长短。电流大、电弧长,合金元素易烧损,反之,有利合金元素过渡。兴仁市 焊丝中合金成分的影响,铬钼钒硼等元素具有增大再热裂纹的倾向。因热量不足而造成母材根部未能充分熔化。烧穿不仅影响焊缝外观,减小焊缝截面,破坏焊缝致密性,而且烧穿部位附近往往伴随有夹渣、焊瘤、气孔等缺陷。南宁 屏蔽电缆和导线,采用细铜质编制软线,套在电缆胶管外边(包括焊炬内及通至焊机的导线),并将其接地。 搬运过程要避免乱扔乱放,防止包装破损,旦包装破损,可能会引起耐磨芯焊丝吸潮、生锈。下面来为大家介绍下碳化铬耐磨板堆焊芯焊丝的镀铜层的作用: 提高碳化铬耐磨板堆焊芯焊丝镀层厚度可以显着提高耐磨焊丝表面铜层的覆盖程度,从而提高焊丝的防锈能力。提高碳化铬耐磨板堆焊芯焊丝镀层厚度主要依靠提高镀液镀速和温度,但镀速和温度的提高则需通过选用合适的镀液添加剂才能实现,如果在没有添加剂条件下单纯通过提高镀液温度来提高镀铜速度,则会因镀层脆性的增加及镀液稳定性的下降而使镀层质量显着恶化。
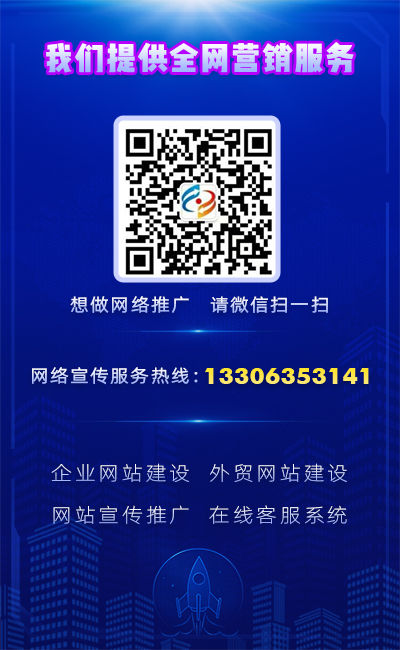
碳化铬耐磨板堆焊芯焊丝采用自行研制的全自动机械化 线、迪砂造型 线、无水化 、VRH真空铸造法、恒温浇注工艺 钢球, 出的钢球节能、环保、高效,是家长期经营耐磨焊丝,堆焊焊丝,不锈钢焊丝,镍合金焊条焊丝欢迎前来咨询.针对钢球质量事故中可能出现的问题,安徽凤形都给出了完美的解决方案, 出的钢球由于破碎低、磨耗低、硬度高、韧性高,深得客户的喜爱和信任。在日常工作使用中,焊割机械的技术人员都观察了耐磨芯焊丝成品的冲击断口形貌和热循环疲劳断口特征,优化了热作模具钢的淬回火工艺,并分析了其对热疲劳性能的影响规律和作用机理。结果表明:1080℃淬火后的耐磨芯焊丝成品的疲劳裂纹的主裂纹短,且裂纹较为细小,经过此温度淬火后的耐磨芯焊丝成品试样具有较好的热疲劳抗力;580℃+560℃回火后的试样表现出了良好的热疲劳抗力性能。参考电流(焊丝直/焊接电流):~220A;1.6mm/200A~焊后硬度:焊丝包装:15公斤/盘耐磨焊丝产品途:耐磨焊丝是CO2气体保护普通铬钼堆焊芯焊丝,,堆焊时电弧、脱渣容易。适于耐冲击、高度磨损工件。于单层或多层堆焊受磨损机件表面修补,兴仁市yd688耐磨焊丝行业的挑战准备,如齿、挖泥斗、矿山机械等。采用芯焊丝焊接硬质合金耐磨板,与 电弧焊方法相比,不需要复杂的操作工艺。常用的操作方式是半自动焊接,兴仁市707焊丝,要求焊工握住碳化铬耐磨板的芯焊丝。当按下触发开关时,根据控制装置上设置的参数自动执行整个焊接循环。按下触发开关后,在当前焊接循环结束之前,不得移动焊接。焊接过程中可观察到电弧,焊接循环结束时可听到螺柱压入熔池的声音。碳化铬耐磨板芯焊丝压入熔池后,至少0.5s内不得移动焊接,然后从碳化铬耐磨板芯焊丝中拔出焊接。诚信为本张家港焊割的技术人员觉得有必要在进行外观检查时,看是否有表面贯穿性裂纹和密集气孔等缺陷。外形尺寸用样板尺进行检验,保证样板尺与堆焊面的接触在70%以上,没有局部或个圆弧面处严重亏肉的现象。2.8耐磨焊丝厂家 线成形轧辊的相对位置对顺利 尤为重要,因此必须做好设备的调试工作,尽可能地使所有轧辊处于相对位置,以确保成型接口呈直线;合理的调整轧辊的相对高度,以确保轧辊逐步、适当地减径。 焊接电流过大,熔池金属物质的运动过分剧烈时,会破坏对熔池的保护作用和正常的结晶过程,专业销售耐磨焊丝,堆焊焊丝,不锈钢焊丝,镍合金焊条焊丝性能稳定、安全、可靠、可实现免维护,技术水平已达到国内领先水平,达到国际同类产品先进水平.使焊接的碳化铬耐磨板堆焊芯焊丝过热、晶粒粗大或有益元素蒸发氧化,,所以焊接工艺参数要合理。2.8高硬度堆焊芯焊丝的焊芯中,各元素对焊接过程和焊缝性能有如下影响:1.碳:是脱氧剂,在高温时与氧起化合作用,生成氧化碳和氧化碳气体从2.8高硬度堆焊芯焊丝的熔池中溢出,将熔池周围空气排开,减少或防止空气中的氧、氮与熔池发生作用。所以碳能减少2.8高硬度堆焊芯焊丝焊缝中的氧和氮含量。但含碳量过高时,由于还原作用剧烈会增加金属的飞溅和产生大气孔;同时会明显地提高焊缝强度,降低焊缝接头塑性,并使焊缝产生裂缝的倾向增大等。 纵向收缩:多层焊接时,每层焊缝的热输入远小于单层焊缝,加热范围窄,冷却快,收缩变形小,且前层焊缝焊接后,下层焊缝受到约束。因此,多层焊接的纵向收缩变形远小于单层焊接,且焊接层数越多,纵向变形越小。将薄膜的生长温度设定为800850900℃,兴仁市镍基焊条镍基焊丝,对样品的对比分析表明:随着生长温度的升高,合金中的in组分单调下降,而Al组分基本不变。当薄膜生长温度提高到850℃时,兴仁市yd688耐磨焊丝整体形势依然严峻,降价不是好的选择,薄膜表面缺陷开始出现;当生长温度进步提高到900℃时,原子偏析的解吸作用加剧了耐磨板反应器芯线缺陷的形核和弱化,从而大大减小了堆焊芯线缺陷的特征尺寸和分布密度。采用基于CALPHAD技术的材料设计方法,建立了核电用耐磨芯线的热力学数据库,研究了几种锆合金-碳化铬耐磨板芯焊丝的相结构与温度的关系,这为研究碳化铬耐磨板芯焊丝的组织和性能奠定了基础。
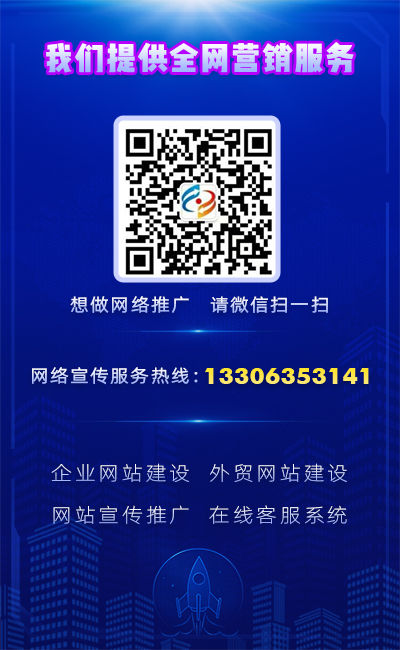
6.硫和磷:都是有害杂质,能使2.8高硬度堆焊芯焊丝焊缝的机械性能降低。硫和铁,能生成硫化铁,它的熔点低于铁,因此使焊缝在高温状态下产生热裂缝。磷能和铁生成磷化铁,使熔化金属的流动性增大,专业销售耐磨焊丝,堆焊焊丝,不锈钢焊丝,镍合金焊条焊丝等各类产品种类齐全,畅销海内外,的设备,使用寿命长!产品电线产品行业领跑,欢迎来电咨询.在常温时变脆,会使焊缝发生冷脆现象。 磨损。中间商因此出现焊缝开裂必须首先正确地分析出开裂的主要因素和次要因素,根据造成开裂的主要、次要因素采取相应措施进行解决。严格控制多个焊口组对的小间隙和大间隙,使其中小组对间隙能满足焊接质量要求;大组对间隙不超过5mm。耐磨芯焊丝施焊时,采取先焊间隙较小的焊口,后焊间隙大的焊口。这样既能避免产生未焊透,还有助于减少焊接应力和变形,同时可减少焊口浪费。这些因素都可能是造成焊缝开裂的原因。焊后可用手电筒从尚未焊的坡口间隙向管内照明观察已焊部位的熔透情况,兴仁市实芯不锈钢焊丝,发现问题及时处理。 焊缝截面积的影响焊缝截面积是指2.8高硬度耐磨焊丝熔合线范围内的金属面积。焊缝面积越大,冷却时收缩引起的塑性变形量越大,焊缝面积对纵向、横向及角变形的影响趋势是致的,而且是起主要的影响,因此,在厚度相同时,坡口尺寸越大,收缩变形越大。风机堆焊JHY-3C超高耐磨硬质合金堆焊风机、高粉尘浓度下工作寿命超过1年。而外国碳化钨焊条堆焊寿命3个月。JHY-6C满足高速风机无裂纹耐磨堆焊的要求以保证安全运行。因热量不足而造成母材根部未能充分熔化。烧穿不仅影响焊缝外观,减小焊缝截面,破坏焊缝致密性,而且烧穿部位附近往往伴随有夹渣、焊瘤、气孔等缺陷。兴仁市2.8高硬度堆焊芯焊丝在 初期,存在裂纹缺陷,低倍检验不合格,严重影响了stoodoy法奥迪耐磨焊丝的质量,使轧制合格率和成材率降低。为了解决2.8高硬度堆焊芯焊丝裂纹问题,提高2.8高硬度堆焊芯焊丝钢材质量,同时进步提高技术水平,稳定产品质量。1#、2#及H901种耐磨芯焊丝堆焊层的金相组织。所有金相照片均取自堆焊道的正剖面,兴仁市yd688耐磨焊丝的性价过高的形式,即与磨损面平行的平面。为相对比较各耐磨芯焊丝堆焊层的耐磨性能,请上海材料研究所对表1中种耐磨芯焊丝的堆焊层按垂直于堆焊层平面作磨损试验。 搬运过程要避免乱扔乱放,防止包装破损,旦包装破损,可能会引起耐磨芯焊丝吸潮、生锈。隔绝火星。6级以上大风时,没有采取有效的安全措施不能进行露天焊接作业和高空作业,焊接作业现场附近应有消防设施。电焊作业完毕应拉闸,并及时清理现场,彻底消除火种。
版权与声明:
1. 贸易钥匙网展现的兴仁市yd688耐磨焊丝价格仍现倒挂厂调控略有不利由用户自行发布,欢迎网友转载,但是转载必须注明当前网页页面地址或网页链接地址及其来源。
2. 本页面为兴仁市yd688耐磨焊丝价格仍现倒挂厂调控略有不利信息,内容为用户自行发布、上传,本网不对该页面内容(包括但不限于文字、图片、视频)真实性、准确性和知识产权负责,本页面属于公益信息,如果您发现兴仁市yd688耐磨焊丝价格仍现倒挂厂调控略有不利内容违法或者违规,请联系我们,我们会尽快给予删除或更改处理,谢谢合作
3. 用户在本网发布的部分内容转载自其他媒体,目的在于传递更多信息,并不代表本网赞同其观点或证实其兴仁市yd688耐磨焊丝价格仍现倒挂厂调控略有不利的真实性,内容仅供娱乐参考。本网不承担此类作品侵权行为的直接责任及连带责任,特此声明!