抚顺东洲区100*16精密钢管厂利润为负停产检修力度加大
发布时间:2020-06-26 06:42:58
发表用户:636HP143272094
浏览量:233
核心提示:抚顺东洲区100*16精密钢管,管坯般为优质的实心圆钢,不同类型的钢管选择的管坯不尽相同,高要求的钢管对应的管坯质量必须相应提高;通过锯切将管坯制作成所需要的长度;通过剥皮将管坯外层氧化皮去除,方便检查外观缺陷,并提高钢管的成材率;环形炉加热需要控制加热温度、加热时间、加
管坯般为优质的实心圆钢,不同类型的钢管选择的管坯不尽相同,高要求的钢管对应的管坯质量必须相应提高;通过锯切将管坯制作成所需要的长度;通过剥皮将管坯外层氧化皮去除,方便检查外观缺陷,并提高钢管的成材率;环形炉加热需要控制加热温度、加热时间、加热速度等工艺参数;加热后的管坯通常由斜轧穿孔机进行穿孔;通过扎管工序,得到优异的金相组织及外形壁厚良好的钢管,扎管设备的种类各异,,根据不同材料和工艺分别选用相应的设备;通过定径工序,钢管将得到更高的尺寸精度和表面质量;管 完成后需要进行涡流探伤或者涡流+超声波的检测方式,探伤合格后的钢管并不代表没有缺陷,只是代表该过程没有发现超出相应要求的缺陷。不锈钢管的种冷轧工艺主要如下:管坯准备→锯切→剥皮→加热→穿孔→切头→酸洗→冷轧→脱脂→热处理→矫直→锯切→酸洗钝化→检验→包装酸洗工序可以去除钢铁表面上的氧化皮和锈蚀等杂质。这个工艺内 的是小直径钢管,所以采用的检验方式是涡流和水压试验。 些工序可以参照热轧的解释。 3特殊用途的钢管和冷轧(拔)钢管壁厚允许偏差可采用绝对偏差。公制焊管:规格用作无缝管形式,用外径*壁厚毫米表示的焊接钢管,用普通碳素钢、优质碳素钢或普能低合金钢的热带、冷带焊接,或用热带焊接后再经冷拨方法制成。公制焊管分普能和薄壁、普通用作结构件,如传动轴,或输送流体,薄壁用来 家具、灯具等,要保证钢管强度和弯曲试验。抚顺东洲区)是制造汽车半轴套管及驱动桥桥壳轴管用的优质碳素结构钢和合金结构钢热轧无缝钢管10.船舶用碳钢无缝钢管(GB5213-8 是制造船舶I级耐压管系、Ⅱ级耐压管系、锅炉及过热器用的碳素钢无缝钢管。碳素钢无缝钢管管壁工作温度不超过450℃,合金钢无缝钢管管壁12.柴油机用高压油管(GB3093-200 是制造柴油机喷射系统高压管用的冷拔无缝钢管。16.常用的轧辊平衡装置有哪几种?阳江冷加工后消除应力退火(BKS)的钢管是在冷加工后进行低温、快速热处理,具有较高尺寸精度和稍高的抗拉强度、定的延伸系数(15%以上)。般用于制造各种机械零件。2.流体输送用钢管(GB/T8163-200 是用于输送水、油、气等流体的般钢管。管坯般为优质的实心圆钢,不同类型的钢管选择的管坯不尽相同,高要求的钢管对应的管坯质量必须相应提高;通过锯切将管坯制作成所需要的长度;通过剥皮将管坯外层氧化皮去除,方便检查外观缺陷,并提高钢管的成材率;环形炉加热需要控制加热温度、加热时间、加热速度等工艺参数;加热后的管坯通常由斜轧穿孔机进行穿孔;通过扎管工序,得到优异的金相组织及外形壁厚良好的钢管,扎管设备的种类各异,根据不同材料和工艺分别选用相应的设备;通过定径工序,钢管将得到更高的尺寸精度和表面质量;管 完成后需要进行涡流探伤或者涡流+超声波的检测方式,探伤合格后的钢管并不代表没有缺陷,只是代表该过程没有发现超出相应要求的缺陷。不锈钢管的种冷轧工艺主要如下:管坯准备→锯切→剥皮→加热→穿孔→切头→酸洗→冷轧→脱脂→热处理→矫直→锯切→酸洗钝化→检验→包装酸洗工序可以去除钢铁表面上的氧化皮和锈蚀等杂质。这个工艺内 的是小直径钢管,所以采用的检验方式是涡流和水压试验。 些工序可以参照热轧的解释。 3特殊用途的钢管和冷轧(拔)钢管壁厚允许偏差可采用绝对偏差。
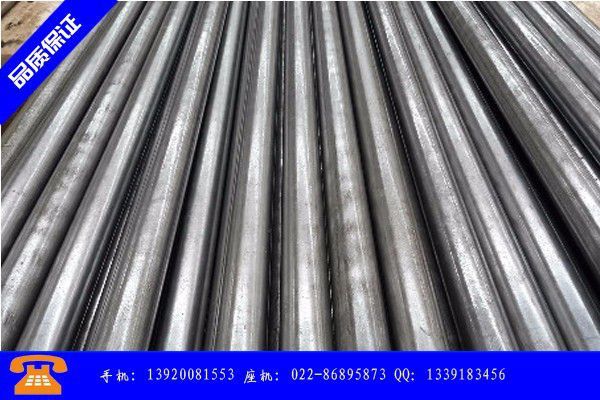
5.承压流体输送用螺旋缝埋弧焊钢管(SY503 是以热轧钢带卷作管坯,经常温螺旋成型,用双面埋弧焊法焊接,用于承压流体输送的螺旋缝钢管。钢管承压能力强,焊接性能好,经过各种严格的科学检验和测试,使用安全可靠。钢管口径大,输送效率高,并可节约铺设管线的投资。主要用于输送石油、天然气的管线。5个。钢管性能优越,金属相对致密。这种穿孔方式使用方坯,穿出的毛管较短,变形量很小,延伸系数般不大于1.1。推轧穿孔的优点如下: 坯料中心处于压应力状态,过程是冲孔和纵轧相结合,不会产生辊斜轧的内折缺陷,毛管内表面质量好,对坯料质量要求较低; 冲头上的平均单位压力比压力穿孔小50%左右,因而工具消耗较小; 穿孔过程中主要是坯料的中心部分金属变形,抚顺东洲区100*16精密钢管怎么判断行为方向,抚顺东洲区100*16精密钢管主要维修技术,使中心粗大而疏松的组织很好的加工而致密化,同时在压应力作用下,毛管内外表面不易产生裂纹。管理钢管的规格通常用外径*壁厚(单位:mm)表示。钢管按 方法可分为热轧钢管和冷轧(拨)钢管两大类。热轧钢管分般钢管,低中压锅炉钢管,高压锅炉钢管、合金钢管、不锈钢管、石油裂化管、地质钢管和其它钢管等。冷轧(拨)钢管除分般钢管、低中压锅炉钢管、高压锅炉钢管、合金钢管、不锈钢管、石油裂化管、其它钢管外,还包括精密钢管、碳素薄壁钢管、合金薄壁钢管、不锈钢薄壁钢管、异型钢管等。热轧管外径般大于32mm,壁厚2.5-75mm,抚顺东洲区90*16精密钢管,冷轧钢管外径可以到6mm,壁厚可到0.25mm,薄壁管外径可到5mm壁厚小于0.25mm,冷轧比热轧尺寸精度高。在管道工程中,管径超过57mm时,常选用热轧管,管径小于57mm时常用冷拔(轧)管。5.承压流体输送用螺旋缝埋弧焊钢管(SY503 是以热轧钢带卷作管坯,经常温螺旋成型,用双面埋弧焊法焊接,用于承压流体输送的螺旋缝钢管。钢管承压能力强,焊接性能好,经过各种严格的科学检验和测试,使用安全可靠。钢管口径大,输送效率高,并可节约铺设管线的投资。主要用于输送石油、天然气的管线。13.性能影响 碳;含碳量越高,钢的硬度就越高,但是它的可塑性和韧性就越差. 硫;是钢中的有害杂物,含硫较高的钢在高温进行压力加工时,容易脆裂,通常叫作热脆性. 磷;能使钢的可塑性及韧性明显下降,特别的在低温下更为严重,这种现象叫作冷脆性.在优质钢中,硫和磷要严格控制.但从另方面看,在低碳钢中含有较高的硫和磷,能使其切削易断,对改善钢的可切削性是有利的. 锰;能提高钢的强度,能消弱和消除硫的不良影响,并能提高钢的淬透性,含锰量很高的高合金钢(高锰钢)具有良好的耐磨性和其它的物理性能. 硅;它可以提高钢的硬度,但是可塑性和韧性下降,电工用的钢中含有定量的硅,,能改善软磁性能. 钨;能提高钢的红硬性和热强性,并能提高钢的耐磨性. 铬;能提高钢的淬透性和耐磨性,能改善钢的抗腐蚀能力和抗氧化作用.为提高的耐腐蚀性能,对般钢管(黑管)进行镀锌。镀锌钢管分热镀锌和电钢锌两种,热镀锌镀锌层厚,电镀锌成本低,所以有了镀锌钢管。
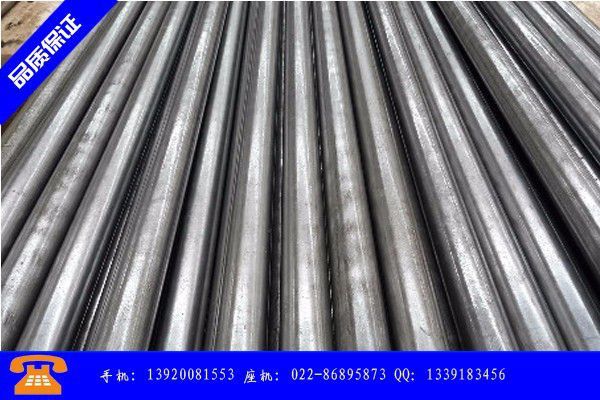
主传动般由主电机或主电极+变速箱组成。详情按 方式:热轧(挤、顶、扩)管、冷轧(拔)管精密无缝钢管是种经过冷拔或热轧处理的高精度钢管材料。由于精密钢管内外壁无氧化层,高压无渗漏,高精度,高光洁度,冷弯无变形,扩口、压扁无裂纹等原因,产品主要用于 气缸、油缸等气动或液压元件,可以是无缝管或焊接管。精密钢管的化学成分包括碳、硅、锰、硫、磷、铬。管坯般为优质的实心圆钢,不同类型的钢管选择的管坯不尽相同,抚顺东洲区6*1精密钢管,抚顺东洲区100*16精密钢管的特色之路,抚顺东洲区25*4精密钢管,高要求的钢管对应的管坯质量必须相应提高;通过锯切将管坯制作成所需要的长度;通过剥皮将管坯外层氧化皮去除,方便检查外观缺陷,并提高钢管的成材率;环形炉加热需要控制加热温度、加热时间、加热速度等工艺参数;加热后的管坯通常由斜轧穿孔机进行穿孔;通过扎管工序,得到优异的金相组织及外形壁厚良好的钢管,扎管设备的种类各异,根据不同材料和工艺分别选用相应的设备;通过定径工序,钢管将得到更高的尺寸精度和表面质量;管 完成后需要进行涡流探伤或者涡流+超声波的检测方式,探伤合格后的钢管并不代表没有缺陷,只是代表该过程没有发现超出相应要求的缺陷。不锈钢管的种冷轧工艺主要如下:管坯准备→锯切→剥皮→加热→穿孔→切头→酸洗→冷轧→脱脂→热处理→矫直→锯切→酸洗钝化→检验→包装酸洗工序可以去除钢铁表面上的氧化皮和锈蚀等杂质。这个工艺内 的是小直径钢管,所以采用的检验方式是涡流和水压试验。 些工序可以参照热轧的解释。 3特殊用途的钢管和冷轧(拔)钢管壁厚允许偏差可采用绝对偏差。抚顺东洲区自动轧管机产生壁厚不均的原因是:穿孔毛管壁厚不均的存在形式和严重程度,直接影响轧后钢管壁厚不均的存在形式和严重程度。 按用途分:锅炉管、油井管、管线管、结构管、化肥管……冷加工/软(BKW)的钢管是通过较小变形量的成品道次冷加工 的,不进行热处理,具有高尺寸精度和较高的抗拉强度、定的延伸系数(10-15%)。般用于制造汽车零件。
版权与声明:
1. 贸易钥匙网展现的抚顺东洲区100*16精密钢管厂利润为负停产检修力度加大由用户自行发布,欢迎网友转载,但是转载必须注明当前网页页面地址或网页链接地址及其来源。
2. 本页面为抚顺东洲区100*16精密钢管厂利润为负停产检修力度加大信息,内容为用户自行发布、上传,本网不对该页面内容(包括但不限于文字、图片、视频)真实性、准确性和知识产权负责,本页面属于公益信息,如果您发现抚顺东洲区100*16精密钢管厂利润为负停产检修力度加大内容违法或者违规,请联系我们,我们会尽快给予删除或更改处理,谢谢合作
3. 用户在本网发布的部分内容转载自其他媒体,目的在于传递更多信息,并不代表本网赞同其观点或证实其抚顺东洲区100*16精密钢管厂利润为负停产检修力度加大的真实性,内容仅供娱乐参考。本网不承担此类作品侵权行为的直接责任及连带责任,特此声明!